3月24日下午,翔正·智造學(xué)堂帶領(lǐng)40余位新時(shí)代制造人,來(lái)到了本次研修課程的終點(diǎn)站東方汽輪機考察和東方電機參觀(guān)。在東方汽輪機的東汽廠(chǎng)史館,了解到東汽在建廠(chǎng)之初,在面臨資金與先進(jìn)設備緊缺的條件下,在廠(chǎng)房基建只完成了65%的情況下,東汽第一批制造人,依然建設出了東汽史上第一臺7.5千瓦汽輪機,更是在1983年創(chuàng )建了我國第一臺具有自主知識產(chǎn)權的30萬(wàn)千瓦的汽輪機。
東汽老一輩制造人,何嘗又不是中國上個(gè)世紀下半葉,諸多領(lǐng)域制造人的真實(shí)寫(xiě)照呢?他們用身體力行,艱苦奮斗,勇于創(chuàng )新的實(shí)際行動(dòng),為中國制造事業(yè)拓荒,而這種拓荒精神,仍然激勵著(zhù)今天由翔正·智造學(xué)堂帶領(lǐng)下的新時(shí)代制造人。他們將繼續傳遞這種拓荒精神,為中國制造事業(yè)的蓬勃發(fā)展,奮斗不息。
在東汽的重型一分廠(chǎng),學(xué)友們不僅看到了整個(gè)西南片區為數不多的12.5m高的大型立車(chē)設備正在加工材料的實(shí)際情況,還了解到了,一臺已經(jīng)使用了半個(gè)世紀的機械加工設備,在經(jīng)過(guò)今天簡(jiǎn)單的數控化改造,依舊能夠使用的情況。
這又再一次印證了第一天在九洲參訪(fǎng)時(shí)了解到的,在數字化轉型改造升級過(guò)程中,并不需要全都購買(mǎi)新的設備,有時(shí)直接改造現有的,就足以支撐。
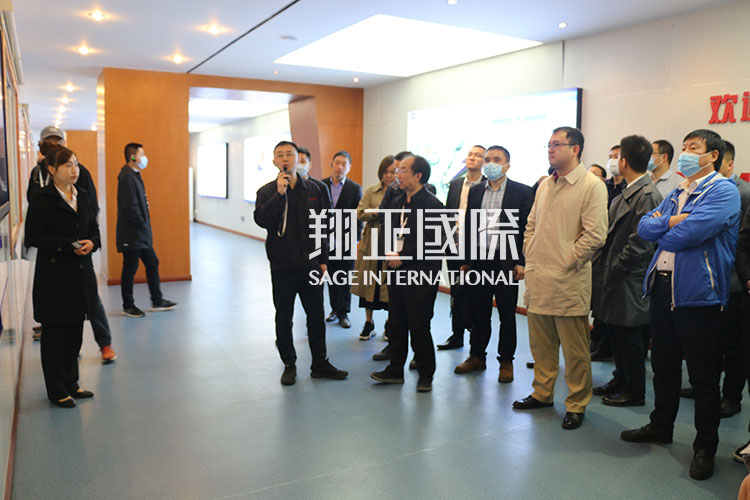
在東汽的葉片加工中心,學(xué)友們揭開(kāi)了作為“華龍一號”核心零部件之一的“1828mm葉片”的神秘面紗,經(jīng)企業(yè)一線(xiàn)負責人介紹,如今的東汽,歷經(jīng)20年篳路藍縷,已經(jīng)從661mm末級阻尼葉片,到當時(shí)世界最長(cháng)的1828mm末級阻尼葉片,再到今天國內最長(cháng)的鈦合金1450mm末級葉片,它已經(jīng)掌握了整套具有自主知識產(chǎn)權的系列化減振阻尼葉片設計關(guān)鍵技術(shù),其設計制造能力,也業(yè)已達到了世界先進(jìn)水平。
但正如古人所云:看似尋常最奇崛,成如容易卻艱辛,就這一個(gè)1828mm末級阻尼葉片,其背后的艱辛與心血,也是令人由衷的敬佩。據東汽的企業(yè)一線(xiàn)負責人介紹1828mm末級阻尼葉片研制過(guò)程中有三個(gè)重要事件:
第一個(gè)事件,是攻克1828mm末級阻尼葉片的關(guān)鍵點(diǎn)的振動(dòng)設計,就這個(gè)振動(dòng)設計,當時(shí)東方汽輪機的相關(guān)工作人員,就每天都要花幾十次的調整。他們要在保證氣動(dòng)性能的前提下,通過(guò)對這些各個(gè)關(guān)鍵部件的不同排列組合,不斷嘗試,對局部葉型優(yōu)化,對拉筋的形式、高度、大小和圍帶減振阻尼結構等進(jìn)行調整,以尋求最優(yōu)的振動(dòng)設計方案。
最終歷時(shí)一年半,他們終于成功完成了對1828mm葉片詳細的氣動(dòng)+強度+振動(dòng)全流程耦合的三維有限元設計分析,為當時(shí)國內最長(cháng)等級1828mm轉子末級葉片的成功自主研發(fā)奠定了堅實(shí)基礎。第二個(gè)事件,是1828mm葉片試驗件進(jìn)入東方汽輪機葉片分廠(chǎng)進(jìn)行加工,這個(gè)加工階段,也是擺在他們面前的一道巨大的難題。當時(shí)他們技術(shù)員們平均每人每天工作12小時(shí)以上,通過(guò)調研、類(lèi)比、頭腦風(fēng)暴等方法,他們擬出了數十個(gè)攻關(guān)點(diǎn),提出了3個(gè)以上的工藝流程方案,歷時(shí)三個(gè)多月,最終才加工成功。
第三個(gè)事件,就是加工完成了,測量又遇到問(wèn)題了,因為加工好的葉片重達256公斤,足足要5個(gè)人,才能抬得起來(lái),因此,極為不便利。為此他們專(zhuān)門(mén)開(kāi)發(fā)了一款新型量具,采取了從立式改成臥式等一系列新型設計,制作出了一個(gè)重達1噸重的量具,直至今日,這個(gè)量具還在使用。正所謂,“逢山開(kāi)路,遇水架橋”,正是由于這樣的思維特質(zhì),才一直激勵著(zhù)東方汽輪機的技術(shù)工人們迎難而上,持續攻堅克難,為我國汽輪機關(guān)鍵技術(shù)的突破做出了卓越貢獻。